324 Lean jobs in the United Kingdom
Manufacturing Process Engineer - Lean Six Sigma
Posted 1 day ago
Job Viewed
Job Description
Key Responsibilities:
- Analyse existing manufacturing processes to identify areas for improvement and efficiency gains.
- Develop and implement process improvements using Lean and Six Sigma methodologies (e.g., Kaizen, 5S, DMAIC).
- Design, test, and validate new manufacturing processes and equipment.
- Create and maintain standard operating procedures (SOPs) and work instructions.
- Collaborate with production, quality assurance, and engineering teams to solve manufacturing challenges.
- Monitor key performance indicators (KPIs) for production processes and implement corrective actions.
- Lead cross-functional teams on continuous improvement projects.
- Troubleshoot production issues and implement root cause analysis to prevent recurrence.
- Ensure compliance with health, safety, and environmental regulations within the manufacturing environment.
- Participate in the evaluation and selection of new manufacturing technologies and equipment.
Required Qualifications:
- A Bachelor's degree in Manufacturing Engineering, Industrial Engineering, Mechanical Engineering, or a related discipline.
- Proven experience as a Manufacturing Engineer or Process Engineer in a manufacturing environment.
- Strong knowledge and practical application of Lean Manufacturing and Six Sigma principles (Green Belt or Black Belt certification preferred).
- Experience with process simulation and CAD software is advantageous.
- Excellent analytical, problem-solving, and critical-thinking skills.
- Proficiency in data analysis and statistical process control (SPC).
- Strong communication, teamwork, and project management skills.
- Ability to adapt to both on-site and remote working environments.
- Must be eligible to work in the UK.
This is a fantastic opportunity for a motivated engineer to contribute to operational excellence in a cutting-edge manufacturing facility.
Senior Process Improvement Engineer (Lean/Six Sigma)
Posted 3 days ago
Job Viewed
Job Description
The Senior Process Improvement Engineer will be responsible for leading cross-functional teams in the identification of process bottlenecks and areas for improvement. You will design and implement Lean/Six Sigma projects, utilizing statistical analysis and data-driven approaches to achieve measurable results. Key responsibilities include conducting process mapping, value stream analysis, and root cause analysis to develop effective solutions. You will develop and deploy training programs on continuous improvement methodologies for various levels of staff. This role requires you to champion a culture of continuous improvement throughout the organization, fostering innovation and problem-solving. You will manage project timelines, budgets, and resources to ensure successful project completion and track the impact of implemented changes, reporting on key performance indicators. Collaboration with operational leaders, engineers, and production staff to integrate best practices will be crucial. The ideal candidate will possess a strong background in industrial engineering or a related technical field, with a minimum of 5 years of experience in process improvement roles, ideally with Black Belt or Master Black Belt certification in Lean Six Sigma. Excellent analytical, problem-solving, and project management skills are essential. You must be adept at using statistical software and process simulation tools. Strong communication and interpersonal skills are required to effectively influence and lead teams remotely. As a fully remote professional, you will need to be self-directed, highly organized, and comfortable using virtual collaboration tools. This is an exceptional chance to make a significant impact on operational excellence and drive transformative change within a globally recognized industrial leader, contributing remotely to projects worldwide.
Lean Consultant
Posted 1 day ago
Job Viewed
Job Description
About SMMT Industry Forum
At SMMT Industry Forum, we partner with organisations of all sizes to deliver complex, transformational change. Our consultants work closely with clients—often embedded within leadership teams—to solve critical challenges and drive lasting impact.
We pride ourselves on building long-term, trusted relationships and only delivering work that truly adds value. That’s why we’re committed to hiring exceptional people who share our passion for quality, integrity, and results.
The Role: Lean / TPM Consultant
SMMT Industry Forum is seeking a skilled and passionate Lean / TPM Consultant to support manufacturing clients in driving operational excellence. This role is ideal for someone with a strong background in continuous improvement, Lean methodologies, and Total Productive Maintenance, who is eager to make a tangible impact across diverse manufacturing environments.
This is a fantastic opportunity to work alongside a team of dedicated professionals and experts that are truly some of the best in their field. This role will require flexibility in working hours, workload and location, as you will be required to travel to the client's location.
The successful candidate will be assigned to execute Training and Consultancy Services delivery on behalf of SMMT Industry Forum.
- Courses to be delivered can be defined as off the shelf training courses (Public and In house), or courses that require special design based on client's needs both Face-2-Face and Virtual
- Consultancy services - based on the clients' needs and subject to qualification/skills match.
Key Responsibilities
- Deliver high-quality training and consultancy in Lean Manufacturing and TPM principles
- Support clients in implementing structured improvement programmes focused on productivity, equipment effectiveness, and waste reduction
- Facilitate workshops and coaching sessions on topics such as 5S, OEE, autonomous maintenance, and planned maintenance
- Conduct assessments, gap analyses, and develop tailored improvement roadmaps
- Collaborate with cross-functional teams to embed sustainable Lean and TPM practices
- Design and deliver both public and bespoke training courses (face-to-face and virtual)
- Provide ongoing support and mentoring to client teams to ensure successful implementation
What We’re Looking For
Essential:
- Proven experience in Lean Manufacturing and TPM implementation within a manufacturing environment
- Experience in automotive, aerospace, defence or high-volume manufacturing sectors
- Strong facilitation and coaching skills
- Ability to analyse data and translate insights into actionable improvements
- Excellent communication and stakeholder engagement skills
- Engineering or manufacturing qualifications
- Willingness to travel and work flexibly across client sites
Desirable:
- World class exposure to lean / operational excellence
- TPM, Core tools, IATF and VDA experience or knowledge
- Certified Lean Six Sigma or TPM practitioner
- Experience delivering training and consultancy services
- Familiarity with digital tools for performance tracking and visual management
Training and Development
No matter your experience or background, you’ll get dedicated support when you join. With an induction and the business's support, you’ll quickly get to grips with the role and have access to help and guidance whenever you need it. So you won’t be on your own – you’ll be a part of a community dedicated to your development.
Rewards and Benefits
- 25 Days Annual Leave and additional days for public and privileged holidays.
- Car Allowance
- Opportunities to be recognised through our employee recognition scheme
- Opportunities to hybrid working, subject to business needs
- Excellent pension scheme
- Cycle to work scheme
- Parental and adoption leave
Culture and Working Environment
As part of our team, you’ll discover an inclusive workplace that’s welcoming, supportive and encouraging. You’ll be part of an organisation where people want to support one another and make a difference. Aside from fostering an open culture, we’ve got a range of growing affinity groups. For example:
- Ethnic Minority and gender equality networks
- Groups supporting wellbeing, mental health, neurodiversity and disability
- Women’s and Men’s Networks
- Faith/No Faith communities for staff to come together
- LGBTQ+ support networks
You’ll also find a variety of social groups to help you settle in and connect with people with similar interests.
Before You Apply
Honesty and integrity are important if you want to work at SMMT Industry Forum. Giving misleading information and omitting or concealing information during the recruitment process is viewed very seriously.
Equal Opportunities
SMMT Industry Forum is an equal opportunity employer and all qualified applicants will receive consideration for employment without regard to race, colour, religion, sex, national origin, disability status, or any other characteristic protected by law. If you need assistance during the application process because of a disability, it is available upon request. The company is pleased to provide such assistance, and no applicant will be penalised as a result of such a request.
We’re Disability Confident
SMMT Industry Forum are proud to have achieved Committed status within the DWP’s Disability Confident scheme. This is aimed at encouraging employers to think differently about disability and take action to improve how they recruit, retain, and develop disabled people. Being Disability Confident, we aim to ensure that we offer inclusive and accessible recruitment. If you require support, reasonable adjustments are available during the application process and if you are successful in joining the organisation.
Eligibility Criteria
We have a legal responsibility to ensure that all our employees have the legal right to live and work in the UK. If we make an offer of employment, we will need to check that you are eligible to work in the UK before you start work. Regardless of an individual’s nationality, race or immigration status, you must provide evidence to us confirming your right to work. This includes British citizens and EU nationals.
Manager - LEAN
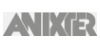
Posted 6 days ago
Job Viewed
Job Description
**Responsibilities:**
+ Responsible for driving deployment and execution of continuous improvement
+ Drive WESCO facilities, offices, and functional areas to achieve world class standards in visual management
+ Establish partnerships with suppliers and customers to achieve continuous improvement across enterprise value stream
+ Mentor senior leadership, vice presidents and directors on role as leaders and promoters of LEAN
+ Provide executive level updates
+ Develop WESCO associates to be self-sufficient in continuous improvement tools
+ Serve as catalyst to promote LEAN thinking and foster continuous improvement culture
+ Promote and supports LEAN self-sufficiency via application of LEAN toolkit, goal deployment, daily management, VoC, etc.
+ Promote out-of-the-box thinking and continuously generates new ideas to improve processes, service, efficiency, inventory, cost and space
+ Assist in development of LEAN Leaders and through personal example, coaching, mentoring, and training
+ Assist and advises field teams to achieve agreed upon performance objectives
+ Lead various events in team settings
+ Select and utilize appropriate LEAN tools
+ Align activities with corporate goals around safety, quality, delivery, cost (SQDC), performs Root Cause Analysis on gaps, rigorously identifies waste, and works with leadership to drive sustainable corrective action
+ Manage kaizen results and action plans
**Qualifications:**
+ Bachelor's Degree - Engineering, Logistics, Technical, or equivalent years of related experience required
+ Licenses/Certificates/Designations - PMP, Change Management or Scrum Master certifications preferred
+ 6 years experience of extensive LEAN leadership , with a medium or large company
+ Highly seasoned and experienced LEAN leader or 6 Sigma Black Belt with a proven track record of end-to-end management of key, strategic programs and business segments (e.g., operations, administration, customer-facing)
+ Strong leadership track record - prior experience in managing teams
+ Extensive experience in managing change and transforming a culture to a continuous improvement mindset
+ Strong track record of accomplishments
+ Solid project management skills and kaizen event experience from initiation through full implementation
+ Strong process orientation and analytical skills
+ Strong written and verbal communication skills
+ Excellent PC skills, including proficiency in Microsoft Office programs
+ Experience with coordinating and optimizing lean tools (visualization, etc.) applications preferred
+ Ability to travel 25% - 50%
_Wesco International, Inc., including its subsidiaries and affiliates ("Wesco") provides equal employment opportunities to all employees and applicants for employment. Employment decisions are made without regard to race, religion, color, national or ethnic origin, sex, sexual orientation, gender identity or expression, age, disability, or other characteristics protected by law. US applicants only, we are an Equal Opportunity and Affirmative Action Employer._
**_Los Angeles Unincorporated County Candidates Only:_** _Qualified applicants with arrest or conviction records will be considered for employment in accordance with the Los Angeles County Fair Chance Ordinance and the California Fair Chance Act._
_#LI-AJ1_
Manager - LEAN
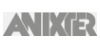
Posted 6 days ago
Job Viewed
Job Description
**Responsibilities:**
+ Responsible for driving deployment and execution of continuous improvement
+ Drive WESCO facilities, offices, and functional areas to achieve world class standards in visual management
+ Establish partnerships with suppliers and customers to achieve continuous improvement across enterprise value stream
+ Mentor senior leadership, vice presidents and directors on role as leaders and promoters of LEAN
+ Provide executive level updates
+ Develop WESCO associates to be self-sufficient in continuous improvement tools
+ Serve as catalyst to promote LEAN thinking and foster continuous improvement culture
+ Promote and supports LEAN self-sufficiency via application of LEAN toolkit, goal deployment, daily management, VoC, etc.
+ Promote out-of-the-box thinking and continuously generates new ideas to improve processes, service, efficiency, inventory, cost and space
+ Assist in development of LEAN Leaders and through personal example, coaching, mentoring, and training
+ Assist and advises field teams to achieve agreed upon performance objectives
+ Lead various events in team settings
+ Select and utilize appropriate LEAN tools
+ Align activities with corporate goals around safety, quality, delivery, cost (SQDC), performs Root Cause Analysis on gaps, rigorously identifies waste, and works with leadership to drive sustainable corrective action
+ Manage kaizen results and action plans
**Qualifications:**
+ Bachelor's Degree - Engineering, Logistics, Technical, or equivalent years of related experience required
+ Licenses/Certificates/Designations - PMP, Change Management or Scrum Master certifications preferred
+ 6 years experience of extensive LEAN leadership , with a medium or large company
+ Highly seasoned and experienced LEAN leader or 6 Sigma Black Belt with a proven track record of end-to-end management of key, strategic programs and business segments (e.g., operations, administration, customer-facing)
+ Strong leadership track record - prior experience in managing teams
+ Extensive experience in managing change and transforming a culture to a continuous improvement mindset
+ Strong track record of accomplishments
+ Solid project management skills and kaizen event experience from initiation through full implementation
+ Strong process orientation and analytical skills
+ Strong written and verbal communication skills
+ Excellent PC skills, including proficiency in Microsoft Office programs
+ Experience with coordinating and optimizing lean tools (visualization, etc.) applications preferred
+ Ability to travel 25% - 50%
_Wesco International, Inc., including its subsidiaries and affiliates ("Wesco") provides equal employment opportunities to all employees and applicants for employment. Employment decisions are made without regard to race, religion, color, national or ethnic origin, sex, sexual orientation, gender identity or expression, age, disability, or other characteristics protected by law. US applicants only, we are an Equal Opportunity and Affirmative Action Employer._
**_Los Angeles Unincorporated County Candidates Only:_** _Qualified applicants with arrest or conviction records will be considered for employment in accordance with the Los Angeles County Fair Chance Ordinance and the California Fair Chance Act._
_#LI-AJ1_
Lean Manufacturing Tutor
Posted 1 day ago
Job Viewed
Job Description
Are you an experienced, recognised and self-employed Tutor and/or Assessors with experience in D32/33/A1/CAVA/TAQA and confident teaching, coaching and delivering apprenticeships in the manufacturing sector?
Approved Training Limited (ATL) are a Grade 2 OFSTED, APAR registered, training provider who are based in the heart of Worcester and operate nationally. We are currently looking to recruit a Specialist Apprenticeship Tutor who will be able to deliver Lean Manufacturing Operative Level 2.
The ideal candidate will have a combination of hands-on experience of the manufacturing/engineering sector, along with apprenticeship delivery experience and you will be responsible for the delivery and monitoring of apprentices to support the development of knowledge, skills and behaviours and to prepare apprentices for the End Point Assessment.
This position can offer hybrid working which is a strong mix of onsite delivery and home-based working. On offer is a salary circa £40,000 per annum (Pro Rata) dependent upon experience, starting off with an initial caseload of 25.
Lean Manufacturing Tutor main duties:
- Delivering apprenticeship standards in Lean Manufacturing Operative Level 2 along with full learner and caseload management
- Proven track record of leadership and ability to inspire and support learners with different abilities.
- Identify and assess learners’ needs and put in place robust learning plans, with realistic and challenging goals, that enable learners to understand their personal journey and realise their potential.
- Build and support work-based projects within the apprenticeship standard
- Actively support, mentor and motivate learners across the entire learner journey, to help them with the timely completion of their learning goals and achievement of their apprenticeship standard.
- Mark work, giving appropriate feedback and maintain records of learner’s progress and development.
- Actively engage the learners “line manager” to enable them to play a proactive role and support the learner to apply their skills in the workplace
- Liaising with and ensuring that the provider is compliant with Ofsted, ESFA, funding partners and awarding organisations.
- Ensuring retention and achievement targets are met.
- Manage and monitor all learner evidence in line with company and awarding body requirements.
- Devise and oversee end point assessment, ensure regular contact with the Quality lead (IV) to ensure quality standards are met.
- Ensure all learners progress through their qualification adhering to schemes of work.
- Maintain regular communication with Key Stakeholders on learner progress.
- Identify and plan additional support for learners, as necessary.
- Ensure Equality and Diversity is embedded and instilled both in and out of the classroom.
- Identify and raise any safeguarding issues to the relevant representative.
- Promote and instil a safe learning environment.
Lean Manufacturing Tutor required skills and experience:
- Hold a recognised Tutor and/or Assessors Award such as D32/33/A1/CAVA/TAQA
- Experience teaching, coaching or delivering apprenticeships in the manufacturing sector.
- Prior experience working within manufacturing and engineering
- Own transport with the flexibility to travel to see learners
- Hold a current DBS check and be registered on the update service
- Ability to facilitate virtual/online training and develop teaching recourses
This position can offer an immediate start for the successful candidate.
If this position sounds like a great career move for you in 2025 then apply now or call directly for more information.
Lean Manufacturing Consultant
Posted 1 day ago
Job Viewed
Job Description
Lean Manufacturing / Supply Chain Consultant (Full-Time Contract)
Location: UK-wide
Daily Rate: £700/day + full expenses + travel
Contact:
Our established Lean consultancy client are committed to helping their clients achieve world-class manufacturing operations by providing high-impact Lean transformational services and delivering sustainable, lasting change. Due to on-going growth, this expanding consultancy now seeks to appoint an experienced Senior Operations Leader / Lean Manufacturing / Supply Chain Consultant on an immediate interim ~6 month basis to lead its premier client transition to an enterprise-wide Lean operating environment.
Our client's holistic approach integrates Lean training, coaching, and mentoring, focusing on strategy, leadership, culture, and operational excellence to achieve sustainable, world-class performance. Working with senior stakeholders (CEO/MD) whilst delivering hands-on coaching to embed lasting change, we seek the following profile:
- Senior Operations / Lean Supply Chain experience driving strategy and measurable bottom-line results.
- Proven continuous improvement expertise in aerospace, automotive, or similar industries.
- A track record of building and leading Lean Production Systems enterprise-wide (to include Procurement / Supply Chain) while mentoring and coaching leaders at all levels.
- Exceptional 'hands-on' leadership, communication, and analytical capabilities.
This full-time contract role till the end of 2025 (with good tailwind to extend) and offers an exciting opportunity to make an immediate and tangible impact.
Interested? To apply, send your CV application to Lean Executives at: quoting reference 0925. Interviews scheduled for 28th August 2025.
Be The First To Know
About the latest Lean Jobs in United Kingdom !
Lean Manufacturing Consultant
Posted 1 day ago
Job Viewed
Job Description
Lean Manufacturing Consultant (Permanent, Full-Time)
Location: UK-wide (Client-facing role. UK travel required 4 nights per week)
Reference: 0825
Contact:
Our established Lean consultancy client is committed to helping organisations achieve world-class manufacturing performance through high-impact Lean transformation services. By integrating strategic guidance with hands-on coaching and mentoring, they deliver sustainable, lasting change across complex operations.
Due to continued growth and client demand, our client is seeking to appoint a permanent, full-time Lean Manufacturing Consultant / Senior Operations Leader to lead enterprise-wide Lean transformations, working with high-profile clients in advanced manufacturing sectors.
Key Responsibilities:
- Lead the development and execution of enterprise-wide Lean operating systems.
- Partner with senior stakeholders (CEO, MD level) to align business strategy with operational execution.
- Deliver coaching, mentoring, and training to embed Lean principles at every level of the organisation.
- Drive cultural and behavioural change to sustain operational excellence and continuous improvement.
Ideal Candidate Profile:
- Extensive senior operations or plant leadership experience with a proven ability to drive strategic change and bottom-line results.
- Deep expertise in Lean manufacturing and continuous improvement, ideally within aerospace, automotive, or similar high-complexity industries.
- Demonstrated success in leading large-scale Lean transformation programmes and coaching leadership teams.
- Exceptional leadership, influencing, and communication skills with a hands-on, results-driven approach.
This is an excellent opportunity to join a respected consultancy and make a tangible impact with clients undergoing transformational change. In return, you will receive a competitive salary package, ongoing professional development, and the chance to shape Lean excellence across top-tier industrial operations.
Interested? Send your CV and salary expectations to Lean Executives at: quoting reference 0825 .
This role requires flexibility and mobility to travel across the UK and Europe in line with client and business needs. There is the potential you may be required to work away from home Monday to Friday, which may include frequent overnight stays. Applicants must be fully comfortable with travel as a core part of the role.
Lean Manufacturing Engineer
Posted today
Job Viewed
Job Description
Key Responsibilities:
- Identify and eliminate waste in manufacturing processes using lean tools and techniques.
- Develop and implement lean manufacturing strategies and projects.
- Conduct process analysis, including Value Stream Mapping and 5S implementation.
- Lead and facilitate Kaizen events and continuous improvement workshops.
- Coach and mentor production teams on lean principles and problem-solving methodologies.
- Analyze production data to identify trends and opportunities for improvement.
- Implement and monitor key performance indicators (KPIs) for manufacturing operations.
- Support the implementation of quality management systems and procedures.
- Collaborate with engineering and production teams to optimize workflows.
- Drive a culture of continuous improvement and operational excellence.
Qualifications:
- Bachelor's degree in Industrial Engineering, Manufacturing Engineering, Mechanical Engineering, or a related field.
- Proven experience (3-5 years) as a Lean Manufacturing Engineer or in a similar continuous improvement role.
- Strong knowledge of lean manufacturing principles (e.g., 5S, Kaizen, VSM, JIT).
- Experience with Six Sigma methodologies and DMAIC is highly desirable.
- Excellent analytical, problem-solving, and project management skills.
- Strong communication and interpersonal skills, with the ability to influence and engage teams.
- Proficiency in CAD software and MS Office Suite.
- Experience in the manufacturing industry.
- Ability to work collaboratively in a team environment.
- Commitment to driving positive change and operational excellence.
Lean Manufacturing Engineer
Posted 1 day ago
Job Viewed
Job Description
Key Responsibilities:
- Lead the implementation of Lean manufacturing methodologies and tools across production facilities.
- Conduct Value Stream Mapping (VSM) exercises to identify bottlenecks and areas for improvement.
- Develop and execute Kaizen events to drive rapid process improvements.
- Implement Six Sigma projects to reduce process variation and defects.
- Analyze manufacturing data to identify key performance indicators (KPIs) and trends.
- Develop and implement standard work procedures and best practices.
- Train and mentor employees on Lean principles and continuous improvement techniques.
- Support the design and layout of efficient manufacturing workflows and cell configurations.
- Drive cost reduction initiatives through waste elimination and process optimization.
- Monitor the effectiveness of implemented solutions and ensure sustainability of improvements.
Qualifications:
- Bachelor's degree in Industrial Engineering, Manufacturing Engineering, Mechanical Engineering, or a related field.
- Proven experience in a Lean Manufacturing or Continuous Improvement Engineering role.
- Demonstrated success in implementing Lean Six Sigma projects and achieving measurable results.
- Proficiency in Lean tools such as VSM, 5S, Kanban, Poka-Yoke, and SMED.
- Strong analytical, problem-solving, and project management skills.
- Excellent communication, facilitation, and training abilities.
- Experience with manufacturing execution systems (MES) and ERP systems is beneficial.
- Certification as a Lean Six Sigma Green Belt or Black Belt is highly preferred.
- Ability to work effectively in a remote team environment and collaborate across different sites.